A Stuttgart melletti központban bepillantást nyerhettünk a fejlesztési folyamatokba és megismerkedhettünk az új One-Twenty megalkotóival.
2006 óta kerékpározom, 2011 óta olvashatók írásaim a Bikemag hasábjain, mégis talán az első alkalmak egyike volt a szeptember közepi kirándulás Magstadba, a Merida európai fejlesztőközpontjába, ahol tabuk nélküli, konstruktív beszélgetést sikerült folytatni egy cég munkatársaival. Az éves bemutató események, mint pl. a ruhpoldingi teszttábor jó lehetőséget adnak az új modellek megismerésére, de kevés részletet tudhatunk meg a technikai háttérről. Más márkánál egy ilyen összejövetelen tesztelték türelmemet azzal, hogy minden technikai kérdésre a következő válasz jött: A mi mérnökeink a legjobbak! Előfordult olyan is, hogy a vacsora utáni négyszemközti faggatáson az elvileg R&D osztályról delegált kolléga kibökte, hogy ő ilyen mélységben nem tud válaszolni a kérdéseimre. Nem titok, hogy két évet én is dolgoztam fejlesztőmérnökként a kerékpáriparban, ezalatt az időszak alatt, talán egyszer kerültem kapcsolatba a médiával, az ilyen irányú kapcsolattartás a marketing osztály feladata.
Ezért is örültem meg kifejezetten a BikeFun Hungary által felajánlott lehetőségnek, aminek célja az európai központ bemutatása volt, a legújabb One-Twenty fejlesztési lépésein keresztül. Az utazás kimenetele az utolsó pillanatig necces volt, de miután a csuklóm összecsavarozását sikeresnek titulálta a Doktor Úr, a tesztelésnek sem szabhatott semmi gátat.
A stuttgarti reptéren Simon Oppold fogadott, ő a teljes Merida & Centurion csoport marketing vezetője, közel 20 év tapasztalattal a kerékpáriparban. A parkolóban be is mutatkozott a régió nevezetessége, vendéglátóm autója mellett egy Porsche GT2 RS parkolt John Player Special festéssel. Az irodába vezető úton bebizonyosodott sejtésem, Németország ezen részén is meglehetősen telített a munkaerőpiac, a friss diplomásokat, főleg a mérnököket és informatikusokat azonnal felszippantják a régió nagyvállalatai, a Bosch, a Mercedes és a Porsche is ezen a környéken tartja székhelyét. Az oktatás minősége tehát kifejezetten magas, az ipari környezett adott, így nem véletlen, hogy a világ egyik legnagyobb kerékpárgyártója itt rendezte be európai R&D központját. A nagyságrendileg 15 fős csapat Jürgen Falke irányításával tervezi a legújabb modelleket. Korábban Röszler Csaba révén nyerhettünk bepillantást a fejlesztés folyamatába.
Az érkezést követően Simon egyből végigvezetett az épületen, a legfelső szinten egy szobában foglalnak helyet a mérnökök és az ipari termék – és formatervezők. Ezt Jürgen Falke irodája köti össze a termékmenedzserek helyiségével. Egy nagyobb bemutató – és tárgyaló rész mellett a felső szinten található a tesztlabor is. Itt prototípusok és szúrópróba szerint kiválasztott gyártásból származó vázak statikus tesztjeit végzik.
A berendezések a Zedler intézet termékei, nyugodtan kijelenthetjük, hogy nevük világszinten etalonnak számít a kerékpár specifikus mérő – és tesztberendezések terén. A fejlesztés során szintén nagy segítséget nyújt a geometria sablon, illetve egy 3D nyomtató is, amivel kisebb tárgyakat, mint pl. papucs vagy himbakar tudnak műanyagból extrúziós technológiával elkészíteni.
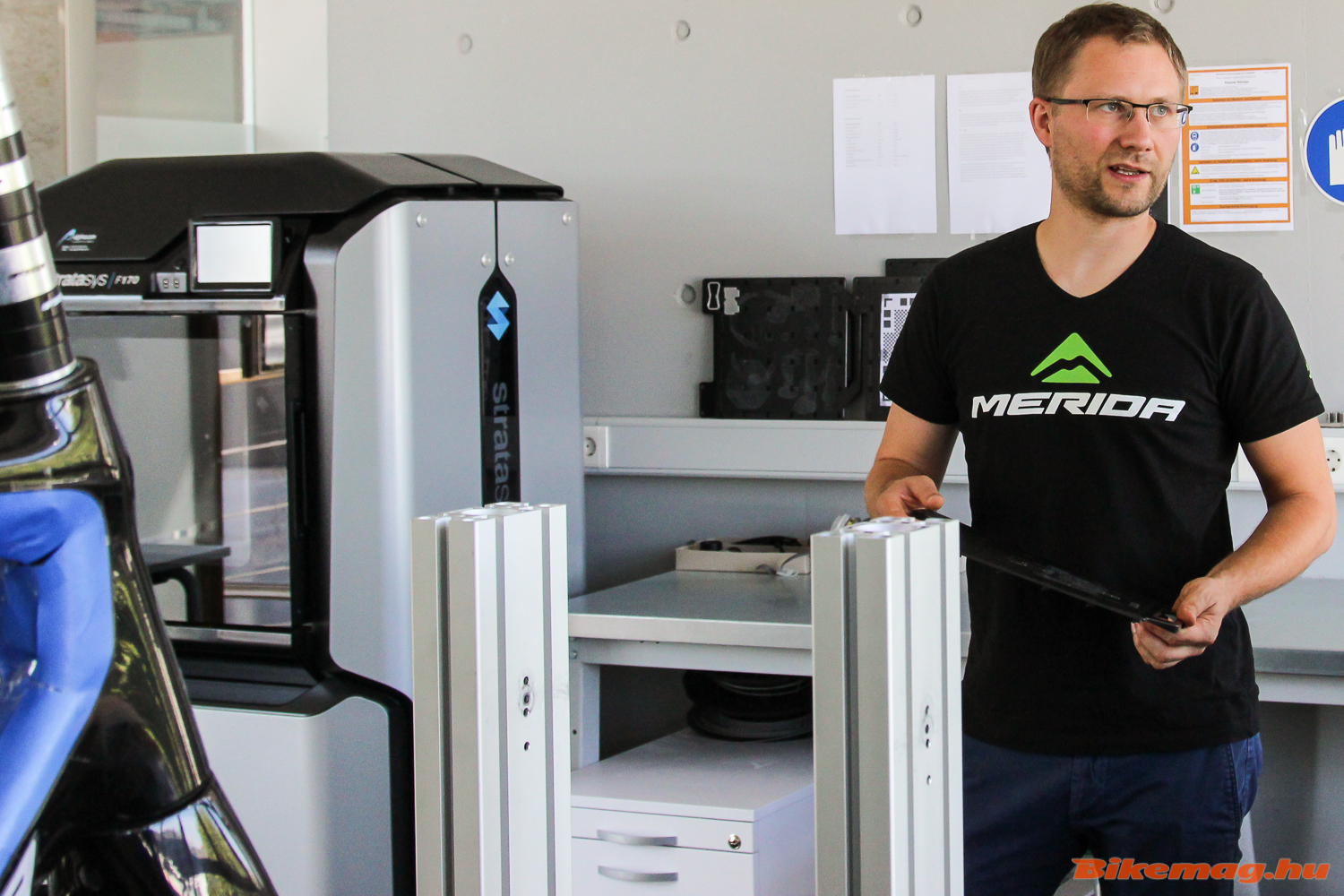
Merida R&D – a 3D nyomtatott prototípus alkatrészek gyorsabbá teszik a fejlesztést
Az alsó két szinten kapott helyet a marketing osztály, a profi csapat (Bahrain-Merida) kapcsolattartója és a könyvelésért felelős kollégák, illetve itt további tárgyalók és kisebb raktárhelyiségek találhatók. A pincében egy teljesen felszerelt műhely működik, egy főállásban és egy félállásban szerelőként tevékenykedő alkalmazottal. A prototípusok összeszerelése és a tesztflotta karbantartása is megoldott ezáltal.
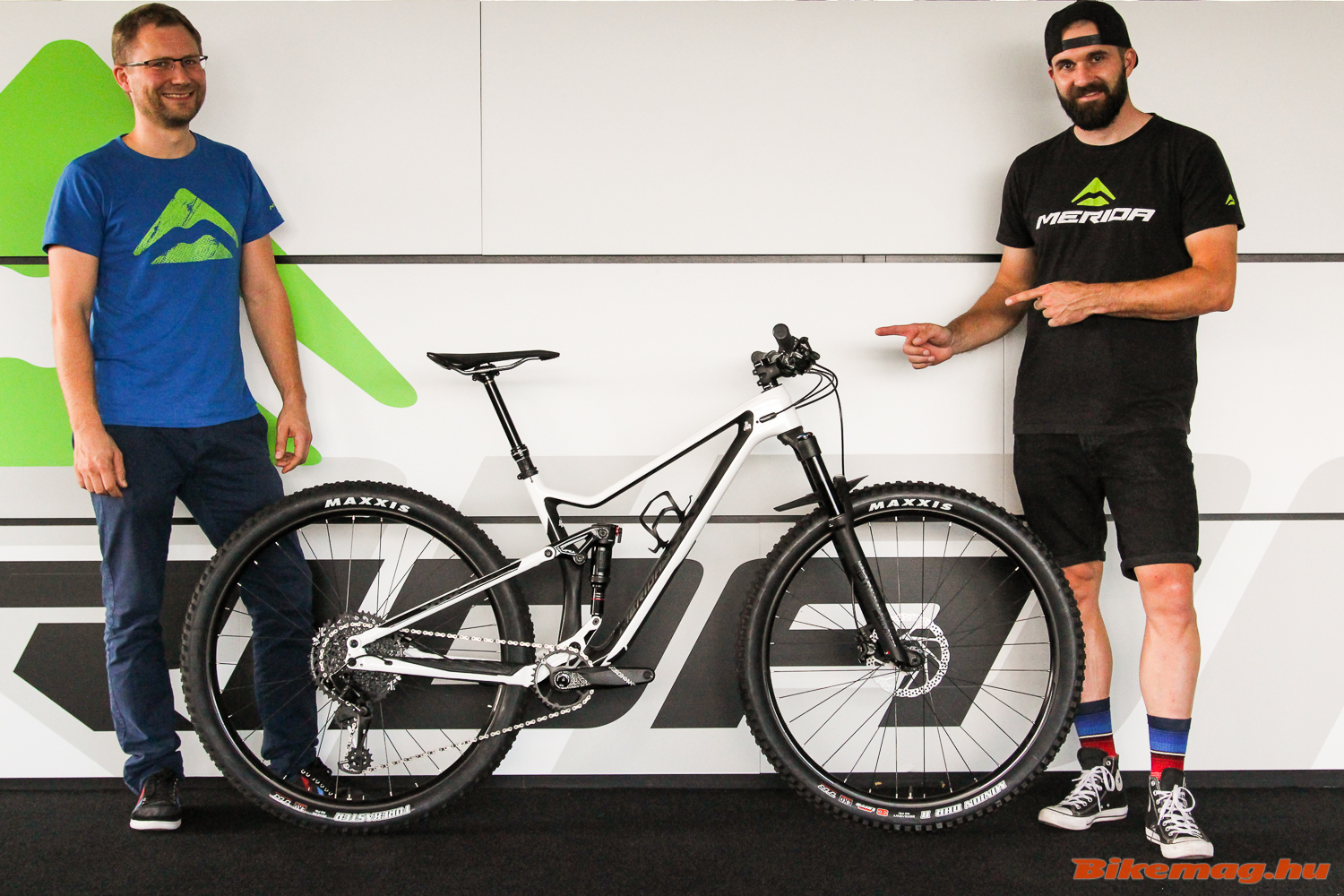
Merida R&D – Roman Braig fejlesztőmérnök és Benjamin Diemer termékmenedzser büszkén mutatták be az új One-Twenty-t
A fejlesztési lépések útvesztőjében ezt követően Roman Braig mérnök és Benjamin Diemer termékmenedzser kalauzoltak tovább elméletben.
Első lépésként meghatározásra kerülnek a leendő modellel szemben támasztott követelmények. A sokösszetevős egyenletben szerepet játszik a felhasználási terület, az ipari trendek, a kereskedők és végfelhasználók visszajelzései és a márka imázsa is. Az új One-Twenty esetében ilyen kulcsfontosságú pontok voltak, a 29”-es kerékméret, az alacsony átlépési magasság, a Trunnion Mount rugóstagokkal való kompatibilitás és a Full Floater kinematika megtartása. Tekintve, hogy a fejlesztési folyamat 2-3 év is lehet, elsőre ez meglehetősen nehéz feladatnak tűnik, de Benjamin elmondta, hogy a beszállítókkal való rendszeres kapcsolattartás sokat segít a jövőbeli terveknél. Már ezen a ponton meghatározásra kerül a geometria, illetve a cég dizájnyelvével összhangba lévő első 3D-s szabadkézi rajzok is megszületnek.
Innentől kezdődik az igazi mérnöki munka, a fejlesztés első fázisában Roman két alapvető dolgot hangol egymáshoz. A felfüggesztés kinematikáját, a forgáspontok helyét a Linkage programmal optimalizálja, míg a 3D-s szilárdtest tervezést CREO-ban végzi. Itt nyilván sok oda-vissza ciklus végbemegy, hiszen egymástól nagy mértékben függő részfolyamatokról beszélünk.
De miért is tartanak ki a Full-Floater kialakítás mellett? Alapvetően egy olyan „négyforgáspontos” (faux bar, linkage driven single pivot), leginkább talán himbarendszer által megvezetett egyforgáspontos rendszereknek fordítható megoldásról beszélünk, ahol a rugóstag alsó pontja sincs fixen a vázhoz rögzítve, hanem a láncvillák meghosszabbításához csatlakozik. Roman elmondása szerint a legfőbb ok, hogy ezzel a kialakítással már rengeteg tapasztalatot gyűjtöttek és pl. egy VPP rendszerre való átállás indokolatlanul elnyújtaná a fejlesztési folyamatot. Ami ennél is érdekesebb, hogy az Horst-Link (FSR) kialakítást egy olyan márka vitte sikerre, aminek napjainkban a Merida komoly hányadban tulajdonosa, így hiába járt le a szabadalom, a leosztás „házon belül” továbbra is megmaradt.
A Full-Floater tehát bevált dolog, és a Linkage program segítségével Roman részletesen elemezni tud minden apró változást. Hajtás közbeni bemozgásra való hajlam, fékfüggetlenség, leverage ratio (a hátsó kerék mekkora elmozdulásához mekkora rugóstag bemozdulás tartozik), ill. ennek függvénye a teljes tartományon, amire olykor progresszivitási görbeként is hivatkoznak.
Ha mindennel elégedett, a 3D-s modell eljut egy valóságban is összeszerelhető szintre és a termékmenedzser által kitűzött geometria is tartható, akkor elkészülhet az első prototípus. Itt nagy segítség a tajvani anyacég, hiszen nem kell külön beszállítókkal egyezkedni, hanem rövid időn belül megérkezik az első minta. Ezekben az esetekben nagyon drága alumínium vázakról beszélünk, mivel a több ezer eurós darabok (1-3) egyes részei (papucs, yoke, himbakar) még CNC megmunkálással készülnek, egyedileg. Ekkor a formázó szerszámok még nincsenek legyártva és véglegesítve, tehát a végső termék máshogy mutat majd, viszont a geometria és a felfüggesztés ellenőrzésére tökéletesen alkalmas egy ilyen „szörnyszülött”. Már az összeszerelés is sok visszajelzést ad, de ezeket a gépeket terepen is tesztelik, több esetben olyan márkanagyköveteket is bevonnak, mint José Antonio Hermida Ramos, vagy éppen a spanyol enduro bajnok Toni Ferreiro. Ha minden klappol, halad tovább a folyamat és megkezdődik a szériaváltozat előkészítése.
A szériagyártásba szánt R&D prototípusok már a végső csőformákkal rendelkeznek, apró fejlesztések történnek még ezt követően. A One-Twenty esetében első körben a forgáspontok szétszereléséhez két kulcsra volt szükség, a csavar tekerésekor az anyát is ellen kellett tartani. Mivel ez megnehezíti a szerelhetőséget, Roman kitalálta, hogy speciális, kör helyett lapított anya esetén a váz is el tudja látni az ellentartó funkciót, így minden forgáspont kötése egy Torx kulcs felhasználásával oldható. Mivel ez a lépés már a sorozatgyártás előszobájának tekinthető (hydroform csövek, kovácsolt yoke és papucsok), a statikus és dinamikus tesztek is megkezdődnek. Előbbi Németországban zajlik, mérik a fejcső merevségét, a középcsapágy merevségét és a hátsó tengelyt terhelve a vertikális komfortot is. Ezek a számok jó visszajelzést nyújtanak a váz várható viselkedéséről. Amennyiben nem teljesen az elvárt eredmények érkeznek, vagy pl. a kitűzött tömeg fölött van a legyártott darab további iterációk szükségesek. A One-Twenty esetében a 3. R&D prototípus már az utolsó volt a széria előtt, célja az előző verzióhoz képest további súlycsökkentés volt.
A dinamikus – és élettartam teszteket Tajvanon futtatják, természetesen az eredmények kiértékelésében a német mérnökök is részt vesznek. Nem egyszerűen az ISO 4210 szabványban meghatározott ciklusok és terhelések kerülnek felhasználásra, hanem sokszor ezek többszöröseit tűzik ki célul a Merida munkatársai. Bizonyos esetekben az anyag kifáradásáig, tönkremeneteléig folytatják a teszteket, hiszen ebből is rengeteg információt lehet nyerni az adott termékről, amit akár a későbbi fejlesztések során is felhasználható.
Ezen a ponton már többen is tesztelik élesben is a gépeket, a rugóstag beszállítókkal megtörténik a kinematikához tartozó végső hangolás, a felszereltségek és a színek is készen állnak a bemutatásra. Elsőként általában a kereskedők látják és próbálhatják ki az újdonságot karöltve a média munkatársaival. Kisebb változtatásokra még ezután is van lehetőség, szerintem meglepődnénk, ha kiderülne mennyi olyan „running change” van kerékpárjainkon vagy éppen autóinkban, amiről végfelhasználóként nem is tudunk.
Karbon váznál az alapok megegyeznek, viszont szilárdtest modellezés helyett a tervezést felületmodellezéssel oldják meg, amiért az ipari termék – és formatervező a felelős. A legnagyobb nehézség itt az, hogy a kerékpáriparban 99%-ban használt „compression moulding” technológia alapfeltétele a meglévő gyártósablon, ami nagyon költséges, így elkészítése előtt érdemes duplán meggyőződni arról, hogy minden tökéletes lesz.
Erre a célra 3D nyomtatott műanyag prototípusokat használnak, amik ugyan nem működőképesek, de pl. a szerelhetőség, a férőhelyek és a formák tökéletesen ellenőrizhetők. A One-Twenty esetén például a nyomtatott vázat bizonyos helyeken még agyaggal tovább tökéletesítették. Ha minden készen áll, a gyártással kapcsolatos tevékenységeket már Tajvan koordinálja, a plybook elkészítése már az ő dolguk.
Az egész bemutatás során átjött, hogy Roman és Benjamin is kifejezetten motivált és szereti a munkáját, ami a legújabb One-Twenty 8000 rövid tesztelésekor is megmutatkozott. Együtt indultunk útnak a Stuttgart környéki ösvényeken, ahol az első pár perc után rögtön sikerült ráéreztem a bringa karakterére.
A 130 mm-es villával szerelt trail változat igazán a gyorsabb lejtőkön érzi otthon magát, kanyarodáskor kifejezetten kívánja, hogy egész testből bedőlve irányítsunk, akárcsak komolyabb lejtőzésre szánt gépek. A rugózás szintén támogatja az agresszív felhasználási módot, 29”-es kerékkel kombinálva nagyon jó a tapadás. A tempónak részemről lefelé az szabott határt, hogy a csuklóm állapota miatt nem tudtam mindig eléggé terhelni az első kereket. A rugózási rendszert felfelé meglehetősen hatékonynak éreztem. Ülve nem, kiállva szándékosan is csak kissé sikerült behintáztatni a rendszert. Az 1×12-es váltórendszerrel átlagos edzettség mellet is könnyedén feljutunk a hegyre, sőt a 12,6 kg-os össztömeg „dropper post”-ot is beleszámítva meglehetősen kedvező. Ha a lejtőkön szerzett élményeket helyezzük előtérbe és nem tervezünk eredménycentrikusan maratonozni, a One-Twenty remek választás lehet.
A közös vacsora alkalmával egy tányér Maultaschen mellett több témát is érintettünk a stuttgarti lakásáraktól kezdve, a helyi ételspecialitásokon át egészen különböző autókig. Mégis valahogy mindig visszakanyarodtunk a kerékpárokhoz. Nem véletlen, hiszen ez számukra nem egy 8-tól 4-ig tartó hivatás, hanem az egész életük e körül forog. Az elmúlt 10 évben rengeteget fejlődött a Merida mind technikai értelemben, mind pedig márkaarculatban. Az európai R&D központban tett látogatást követően nincs kétségem miért.
A Merida kerékpárok hazai forgalmazója: BikeFun.hu
BikeFun Hungary Facebook