A kétrészes interjúban bemutatott amerikai ENVE Composits kétségtelenül a karbonalkatrészek Rolls Royce-ja, kompromisszummentes hozzáállásukkal folyamatosan a karbontechnika határait feszegetik. A Two Johns podcasban elhangzott interjú első részében Jason Schiers a cég alapításáról, filozófiájáról, illetve a leghíresebb termékeikről, a karbon abroncsok technológiai sajátosságairól beszélt. A második részben több mindent érint a beszélgetés: a kerékpáriparban etalonnak számító ENVE villákról is lesz szó, de kitér a tárcsafékekre, illetve a karbontechnika egyéb rejtelmeire is.
Ha meg szeretnétek nézni, hogyan készülnek az itt szereplő termékek, íme a link! http://www.bikerumor.com/2012/05/17/enve-composites-factory-tour-inside-look-at-company-carbon-fiber-manufacturing/ További info pedig: http://www.enve.com/
Two Johns: Azt mondtad, hogy a karbonszerkezetek esetében a gyártás során alkalmazott technikai eljárás fontosabb, mint maga az alapanyag. Ez minden karbonalkatrész esetében igaz, vagy csak a korábban taglalt kerékszettekre?
Jason Schiers: Bár nem próbáltuk ki, de egészen biztos vagyok abban, hogy ha az EDGE berendelne 30 tonnás szakítószilárdságú, általános felhasználásra gyártott, olcsó impregnált szövetet – amelynél különben legalább kétszer erősebbet és jóval költségesebbet alkalmazunk -, az alapanyag függvényében kicsit módosítanánk az általunk alkalmazott technológián, optimálisabb karbonszerkezetet tudnánk létrehozni, mint a legtöbb gyártó a ma kapható legerősebb, legdrágább típusból. Ez minden karbonszerkezetre, vagyis a kerékpár esetében -alkatrészre igaz, persze bizonyos alkatrészeknél fokozottan jelentkezik, másoknál az alapanyag-választásra is oda kell figyelni, főként a merevség vagy éppen a rugalmasság biztosítása érdekében.
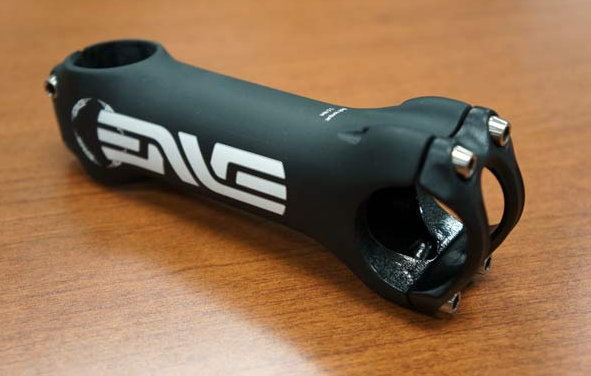
Egyedül a kormányszárral nem tudott sok mindent kezdeni az ENVE – azért kínálnak egyet 125 grammos tömeggel, páratlan merevséggel és kényelemmel…

A nyeregszár esetében ellenben nagyon megéri karbonból dolgozni, ráadásul a kényelem is “tuningolható”…
Two Johns: Van-e olyan kerékpáralkatrész, amelyhez a karbon nem éppen ideális alapanyag?
Jason Schiers: Igen van, de nem sok. Általában elmondható a karbonszerkezetekről, hogy ha megfelelő tervezést követően magas technikai színvonalon történik a gyártás, akkor könnyebb és erősebb lesz az alkatrész, mint bármilyen fémes alapanyagból előállított változat. Továbbá – és ami a legfontosabb – mechanikus tulajdonságai, terhelés alatti viselkedése tág keretek közt optimalizálható. Fejlesztéseink során egyetlen olyan alkatrésztípussal találkoztunk, ahol ha megszakadtunk, akkor sem voltunk képesek lényegesen jobb szerkezetet alkotni, mint a fémes alapanyagú alternatíva. Ez a kormányszár. Felépítése rendkívül egyszerű, és maximálisan adja magát a fémmegmunkálásra, de a két bilincs és a bennük lévő menetkialakítás miatt körülményes a karbon alapanyag használata, különösebb előnnyel nem jár
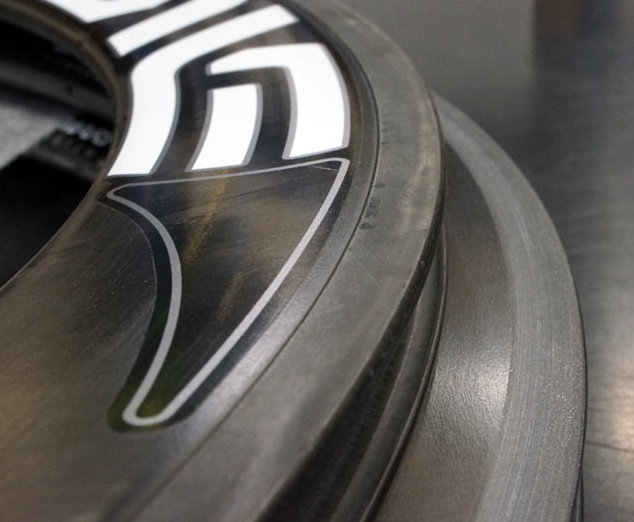
A szingós felnik esetében is ki kellett fejleszteni az ideális fékezőfelületet: a tárcsafék ezt is a problémát is megoldja…
Two Johns: Korábban szó volt a selejtszámról. Ti mekkora selejtaránnyal dolgoztok?
Jason Schiers: A kompozitszerkezet-gyártás rendkívül nagy szakértelmet, kézügyességet igénylő, döntő részt manuális munka. Nehezen automatizálható, az ilyen irányú próbálkozások általában megbuknak. Éppen ezért a selejtszám is nagyobb, mint a fémes alapanyagok használata során. 5 év kemény munkával értük el azt, hogy az üzemünkben készült termékek selejtaránya 5% alá csökkenjen. A kezdetekkor ez ennek közel tízszerese volt! De ehhez hozzá kell tenni, hogy nem minden gyártó alkalmaz egyforma minőségellenőrzés-protokolt, illetve azt nem nem egyenlő szigorral kezelik.
Two Johns: Szerintem a következő kérdés is végeredményben a karbonszerkezettant érinti. Szerinted elterjed-e a tárcsafékek használata az országúti kerékpárok esetében?
Jason Schiers: Mindenképpen, és ez leginkább a ma még kevésbé elterjedt peremes karbonabroncsok előtt nyitja meg az utat. Az abroncsfék alkalmazása számos problémát vet fel az abroncstervezés és gyártás területén. Meg kell oldani a hőelvezetést, amely a peremek, illetve a szerkezet miatt igen nehézkes. Amiért ezek a felnik ma nehezek, drágák és nem teljesen megbízhatók, abban keresendő, hogy a hőtermelés miatt magasabb hőfokra optimalizált lamináló anyagot kell használni, amely még extrém használat mellett sem olvad meg. Természetesen ilyenből rengeteg -féle létezik, ezeket használják többek közt a repülőgép- és az űriparban, de mindnek közös tulajdonsága, hogy kizárólag rideg szerkezet hozható létre belőle, amely egy kerékpárabroncs esetében a legkevésbé kívánatos. A karbonfelnigyártók ma kötéltáncot járnak: olyan lamináló anyagot választanak, amely remélhetőleg nem lágyul vissza a hosszabb lejtmenetek során sem, de kellően duktilis, azaz rugalmas és kifáradásra nem hajlamos, hogy megbízható, jó menettulajdonságokkal rendelkező kereket eredményezzen. Nehéz feladat, nincs még meg a tökéletes megoldás. Ellenben ha a fékezést az abroncstól eltávolítjuk, a tervező keze szabad, egyszerre lehet a peremes kompozitabroncs könnyű, tartós, stabil és megbízható. Elképzelhető, hogy a tömegkülönbség a szingóshoz képest csupán néhány százalék lesz – ma ez minimum 15-20% -, a kerék mindennapi használata praktikus, azaz defekt esetére nem szükséges pótköpenyt cipelni. Ezt is lehetővé tenné az országúti tárcsafék elterjedése, amellett, hogy, a fékerő rendkívül pontosan adagolható, használata pedig időjárás-független. Ez utóbbi a mai szingós karbonabroncsokat is érinti: lévén számunkra rendkívül nagy kihívás volt olyan fékfelületet kialakítani, amely bármilyen körülmények közt megbízható és megfelelő fékhatást biztosít.
Two Johns: Számomra az első villa egy lenyűgöző alkatrész: több irányból érkező erőknek kell ellenállnia, stabilitást kell nyújtania, de ez nem mehet a kényelem rovására. Kérdeznélek, hogy szerinted milyen a jó karbonvilla, milyen érdekes technológiákat lehet itt alkalmazni?
Jason Schiers: A villa valóban egy trükkös alkatrész, az általad említett dolgokhoz még az is hozzátartozik, hogy egy esetleges törésnek itt nagyon csúnya következményei lehetnek. Amikor mi megterveztük az első villánkat, a gyártók egytől egyig előre elkészített karbonnyakkal dolgoztak, amely köré építették a két villaszárat, a nyak aljába pedig egy csomó karbonszállal megerősített kompozitgyantát tömtek. Ezt pedig átfúrták, hogy a villa a féket fogadja. Szerkezetet szempontjából nem éppen ideális, ráadásul a szár alján lévő saru is külön egység volt – általában alumínium – ez is ragasztással került a helyére. Nem volt homogén, sem különösebben erős, de gyártása gyors volt és költséghatékony. További jó tulajdonsága az volt, hogy maga a fékrögzítő csavar mechanikusan is összekapcsolta a nyakat a szárakkal, így a legtöbb esetben a szerkezet végeredményben megbízhatónak bizonyult. Mi teljesen más szemszögből közelítettük meg a feladatot. Először létrehoztuk azt a szerszámot, amely képes egyetlen egységként létrehozni a villát, beleértve a fent említett nyakat, sarukat, illetve a „beépített” féktengely-nyílást. A karbonszálak a villa teljes hosszában, a nyak tetejétől a saruig futnak. A terhelés a villanyak és a -szár találkozásánál összpontosul, ott kell, hogy a szerkezet a legerősebb legyen. A mi villánk esetében a villában található minden egyes szál áthalad, egyfajta harmóniát alkotva, rendkívül erős, könnyű, egyszóval optimális szerkezetet alkotva. Minden egyes szálnak funkciója van, egyik sem felesleges.
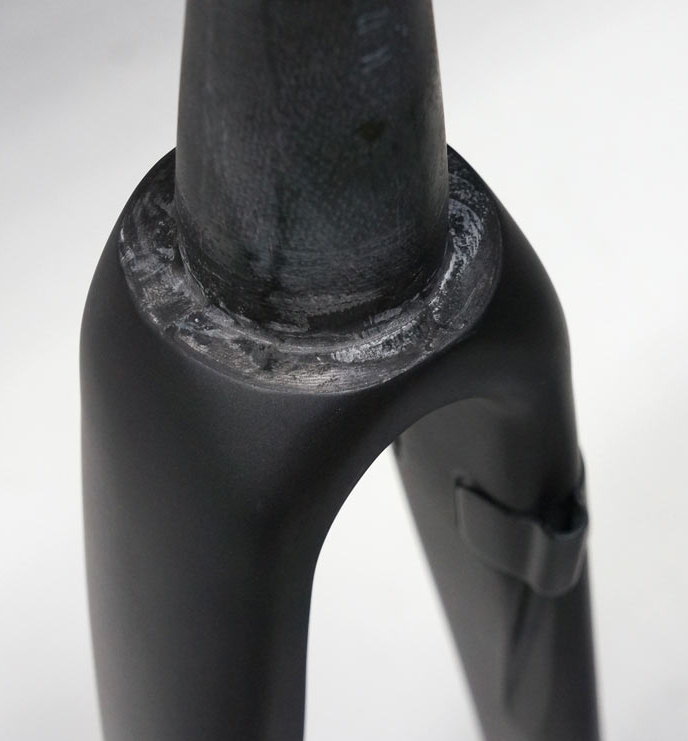
A villa egyetlen, folytonos, harmonikus egységet képez, nincs rajta se ragasztás, se fúrás, minden karbonszál a nyak tetejétől a saruig fut, és mind áthalad a terhelés szempontjából kritikus vállrészen…
Two Johns: Van-e értelme a ma igen divatos megnövelt alsó csapágyméretnek?
Jason Schiers: Mi örültünk ennek a trendnek, mivel a „szűk keresztmetszet” a villavállnál nagyobbá vált, így könnyebb lett a szálak elvezetése. De hozzá kell tenni, hogy mi az alul-felül 1 1/8”-os nyakkal is képesek voltunk teljesíteni a legszigorúbb biztonsági követelményeket, villánk tömege jóval 300 gramm alatt maradt, és mind a profi, mind az amatőr használók rendkívüli stabilitásról és kényelemről számolnak be. A többi gyártónak ez a méretnövelés más előnyöket hozott, mint nekünk: ott részben a stabilitást növelte, amit a könnyű villák esetében sokan hiányoltak, másrészt a kerékpáriparban megszigorított biztonsági teszteket villáik csakis így voltak képesek teljesíteni. A villák könnyebbek lettek, stabilabbak és biztonságosabbak. Az alsó nyakátmérő ezután tovább növekedett, mivel így a fenti előnyök fokozhatók voltak. Sajnos ma már kormánycsapágyszabványról nem is beszélhetünk, annyi -féle és fajta létezik. A mi villáink esetében már az első méretnövelés, azaz az 1 ¼” is elegendő volt a praktikusabb gyártástechnológia alkalmazásához, de bármilyen meglévő vázhoz passzoló villatípust kell kínálnunk […] és ehhez jön a cyclocross típus ugyancsak három méretben, majd az MTB rövid és hosszú ugyancsak háromban… ez mind mind külön szerszámot igényel, azt le kellett gyártani, tehát nekünk anyagilag nem igazán érte meg a megnövelt alsó csapágyméret trend. […]
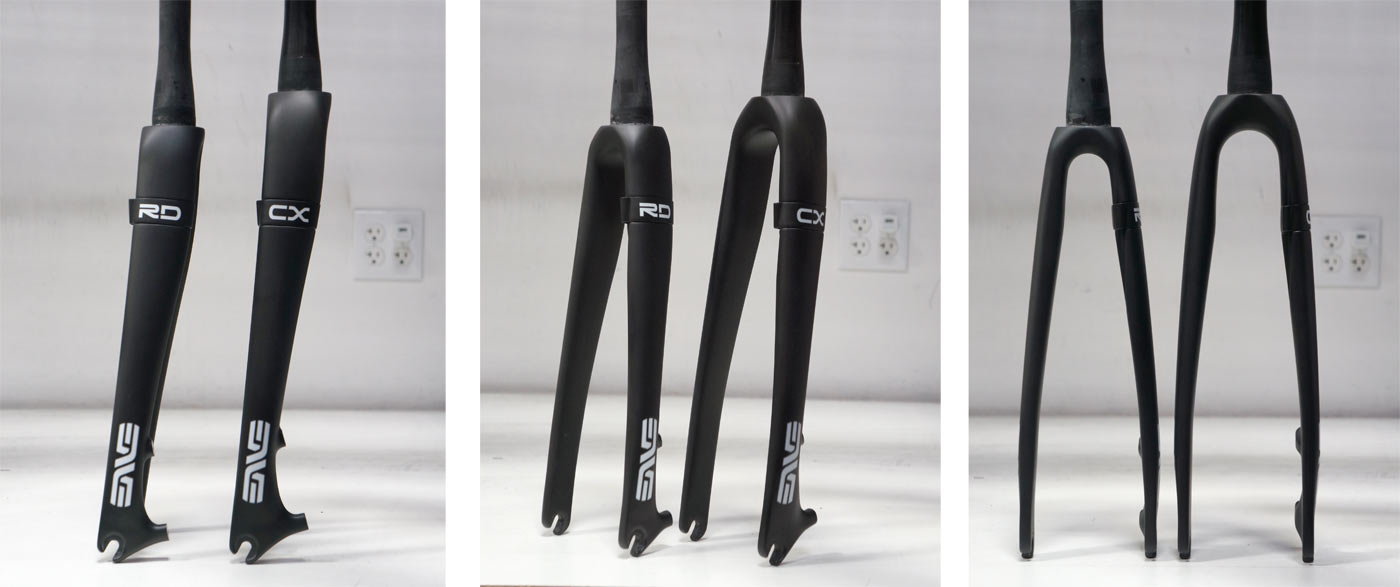
Többféle felhasználásra, többféle nyakszabvánnyal: mivel nem külön egységekből épül fel, az ENVE-nél mind külön-külön szerszámot igényel…
Two Johns: Szerinted mi a kompozitalkatrész-gyártás legnagyobb kihívása?
Jason Schiers: Az utóbbi öt évben az ENVE fejlesztéseivel és a gyártástechnológiáival minden szempontból a végletekig ment: úgy látom, hogy mára már feltérképeztük a határokat. Számos problémát kellett eközben megoldani. Többé-kevésbé tisztában vagyunk azzal, hogy milyen általános karbontechnikai fejlesztések szükségesek ahhoz, hogy tovább lehessen lépni. Továbbra is szeretnénk a karbonalkatrészek úttörői lenni, amelyhez ez az ismeret elengedhetetlen. A fejlődés egy folyamat, egy út, amely az ismeretek elsajátításának fokozatos módja, de nincs végső célja. Kultúránk szerves része, hogy szeretnénk minél többet megtudni mindenről, ami minket körülvesz. Mi a karbonszerkezeteket tűztük zászlónkra, ezt próbáljuk a lehető legmagasabb szintre fejleszteni, a lehető legjobb megoldásokat biztosítani, minden más karbonfejlesztő előtt járni. Tudjuk, hogy nincs tökéletes karbonszerkezet, lévén a világ folyamatosan változik, fejlődik.
Two Johns: Köszönjük a beszélgetés, sok sikert a további munkához!
Jason Schiers: Köszönöm a lehetőséget, hogy beszélhettem a cégünkről, illetve elképzeléseinkről.
Forrás: Two Johns podcast
Szerk. Németh Balázs
Fotó: ENVE
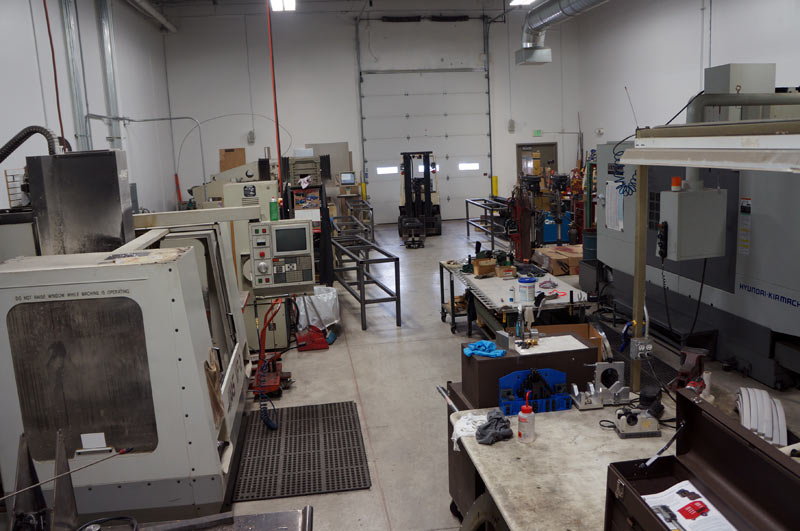
CNC gépek egymás hegyén hátán: helyben készülnek a karbonalkatrészgyártáshoz szükséges szerszámok is!