Régóta terveztük már ezt a cikket. Mindig is kíváncsi voltam rá, hogy mi is rejtőzik a csillogó felszín alatt. Vajon a tetemes árcédula ténylegesen azt takarja, mint amit a marketingszlogenek ígérnek? Mulder és Scully ügynökök óta már tudjuk, hogy „Az igazság odaát van”. Így hát belevágtunk – szó szerint… Minden 1990-ben kezdődött a Kestrel CSX-el.
Ez volt ugyanis első széria karbonváz, illetve kerékpár, mely természetesen ekkor még elég sok gyermekbetegséggel küzdött. Aztán 1993-ban már a Trek is beállt sorba, rögtön túl is lépve az alumínium muffos, ragasztott karboncsöves technológiát, létrehozva az OCLV-t, mely ugye az optimális sűrűség/kevés hézag rövidítése volt, 1% alatti légbuborék tartalommal. (az amcsi hadiipari szabványban 2% alatti bubi tartalom az elvárás) Néhány év alatt szinte egyeduralkodóként dominálták a karbonvázak piacát, mivel ekkoriban minden konkurensük alumíniumvázak fejlesztésével foglalatoskodott, meglehetősen veszett tempóban.
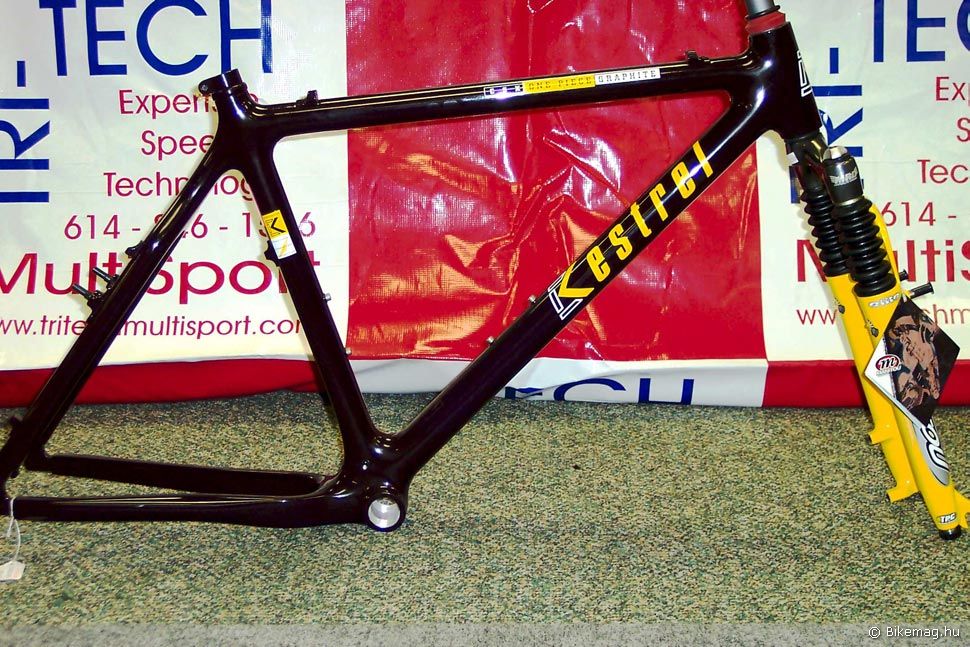
A karbonvázak egyedisége abban rejlik, hogy a hagyományos fémből készült vázakhoz képest jóval többféle módszerrel lehet az elemi szálból vázat kreálni.
Jó néhány évnek el kellett telnie ahhoz, mire rájöttek a többiek, hogy elég nehézkes az akkori technológiákkal 1400 g alá menni az alumíniumvázak terén, ráadásul úgy, hogy az emellett több évig működőképes maradjon. Nagyjából ekkor szállt fel szinte minden kisebb és nagyobb gyártó varázsütésszerűen a „karbonvonatra”, ami azóta is egyre nagyobb sebességgel robog.
Első blikkre talán azt gondolhatná az ember, hogy ha már közel 20 éves történelme van a karbon kerékpáripari alkalmazásának, akkor nagy valószínűség szerint minden karbonváz és alkatrész automatikusan egy nagyon magas minőségi szintet képvisel. Ki kell hogy ábrándítsunk mindenkit, de ez sajnos nincsen így. Itt is igaz, hogy a gyártó cégek egyik célja, hogy minél jobban kinéző portékát értékesítsenek minél magasabb áron, a még éppen elégséges műszaki tartalommal, mivel így lehet maximalizálni a profitot. Elég csak végignézni bármelyik kerékpáripari szakkiállításon, mindenki mindent karbonból készít, még akár egy garázsban is. Ezen alkatrészek némelyike nehezebb, drágább és gyengébb, mint ha éppenséggel nem karbonból lenne. Természetesen kivételek is akadnak bőven. Szerencsére van azért jó néhány gyártó, melyek mögött kellő tőke és elszántság áll, hogy pénzt és időt nem kímélve kifejlesszenek valami olyat, ami tényleg magas színvonalú.
Úgy gondoljuk, hogy az alábbi három gyártó ezt a szintet képviseli, annak ellenére is, hogy mindhárom váz elképesztően különbözik egymástól.
A karbonvázak egyedisége abban rejlik, hogy a hagyományos fémből készült vázakhoz képest jóval többféle módszerrel lehet az elemi szálból vázat kreálni. Minden módszernek van előnye és hátránya, ezért abszolút üdvözítő megoldásként egyiket sem lehet kikiáltani. Tovább bonyolítja a helyzetet, hogy az egyes gyártástechnológiák akár kombinálhatók is egymással, tovább nehezítve így a döntést, hogy akkor most melyik megoldás is a legjobb.
A legnagyobb nehézség a történetben, hogy a gyártók ezen technológiákból a lehető legkevesebbet kommunikálnak kifelé, így a fogyasztói szempontból nem marad más, mint a tömeg, az ár, a gyártóba vetett bizalom és a kinézet alapján való döntés. Az utóbbi, az esetek egy részében köszönő viszonyban sincs a beltartalommal és a valós teljesítménnyel.
Mielőtt belevágnánk a sűrűjébe, kiindulási alapként tisztázzuk az egyes gyártástechnológiai eljárások alapjait.
Négyféle fő technológia alakult ki az elmúlt évek során:
1. Muffolt, avagy illesztékes technológia:
Az úgynevezett muffok segítségével ragasztják egymásba a külön-külön elkészített csöveket, illetve csőkapcsolatokat, majd ezt az egészet általában beborítják még néhány réteg extra szövettel. A technológia ismert képviselője a TREK OCLV váz, csak éppenséggel ők az egészet nem vonták be még egy plusz réteg szövettel. Az ilyen vázak a csővégeken fellépő dupla falvastagságok miatt általában merevebbek, erősebbek, de egyben nehezebbek is, mint a „cső a csőhöz” jellegű vagy monocoque vázak. A teljes egészében, vagy részben muffolt váz még ma is viszonylag elterjedt gyártási eljárás, főleg a középkategóriás vázaknál. A technológia hátránya, hogy minden egyes vázmérethez több muffsablont kell legyártani, így meglehetősen szerszámigényes a folyamat. A technológia előnye, hogy mind a muffok, mind pedig a csövek külön kerülnek legyártásra, van több nyitott végük is, így a gyártási folyamat alatt a szálak elhelyezkedése viszonylag jól kordában tartható. Az eljárásnál természetesen karbon muffokat használnak, a korábbi alu illesztékekbe ragasztott karboncső korszaka már lezárult.
2. Monocoque:
Az igazi monocoque vázak egy darabból készülnek. A gyantával átitatott karbonszálakat egy felfújható tömlő köré tekerik, amelyet aztán két negatív félforma közé helyeznek. Az összezárt formában felfújják a szilikon vagy nylon tömlőket, mely a forma falához préseli a szálakat, kiszorítva közülük a felesleges műgyantát. A sütés során a tömlő nyomás alatt áll, így nyeri el a váz a végleges formáját, szilárdságát. Ez a technológia drága, emellett pedig nagyméretű sütőformákat és sok kézimunkát követel meg. Előnye, hogy vázméretenként csak egy formára van szükség, hátránya, viszont, hogy az „egylépéses” sütési folyamat alatt nehéz kontrolálni, hogy a zárt formán belül minden az előzetes tervek szerint alakuljon.
3. „Cső a csőhöz”:
Ez az eljárás hasonlít leginkább a hagyományos fémből készült vázaknál megszokott eljárásokhoz. Ennél a módszernél a normál alu- vagy acélvázakhoz hasonlóan minden cső előzetesen legyártásra és megmunkálásra kerül. Az előre gyártott csöveket lépésről lépésre megmunkálják, a végeiket egymáshoz igazítják, majd ragasztják, végül pedig a kialakult kötést és környékét újabb rétegekkel vonják be. E metódus előnye, hogy kevés anyagból nagyon merev váz gyártható, amely rendszerint igen könnyű is, mivel minden felesleges anyagtöbblettől mentes. További előny, hogy az alapelemek két nyitott csővége miatt a gyártási folyamat során jól kontrolálható a szálak elhelyezkedése, emellett nem is igényel olyan méretű és mennyiségű költséges szerszámot, mint az előző két eljárás. E technológiát a Scott fejlesztette ki, de manapság már egyre több gyártó (pl. a Specialized) alkalmazza ezt az eljárást, mivel a legkönnyebb vázakat így lehet létrehozni. A csúcskategóriás vázak nagy része ma már így készül.
4. Hibrid eljárás:
A közép-felső kategóriás vázak gyártási metódusa. Lényege, hogy mindenhova a legideálisabb módszert választják a fentiek közül: a középrész pl. monocoque, a fejcsőnél „cső a csőhöz” technológiát alkalmaznak, míg a papucsnál muffolással dolgoznak. E megoldás lényegi eleme a költséghatékony gyártási eljárás, és emellett a kiemelkedő teljesítmény.
Az elméleti fejtegetés után térjünk is át gyorsan a gyakorlatra!
Ha ki akarjuk deríteni a valóságot, akkor két út áll előttünk. Gyárthatunk mérőberendezéseket, melyekkel a terhelt vázakon kimérhető, hogy mely vázak hogyan reagálnak bizonyos terhelésekre, erőkre. E módszer alakul át idővel töréstesztté, ha nem kapcsolják ki időben a gépet… A mérési eredmények egymással jól összehasonlíthatók, de az ilyen teszteket célszerű kiegészíteni tényleges kipróbálással, mert gyakran a mérések eredménye szöges ellentétben áll a bicajosok által érzékelt és megérezhető menettapasztalatokkal. Mi nem ezt a módszert választottuk…
A különböző gyártási eljárásokhoz legyártott ideológiáknál szerintünk sokkal többet árulnak el a vázak belső, szétvágás nélkül láthatatlan részei. A következő oldalakon három gyártó felboncolt vázait találjátok. Mint látható, minden csövet átvágtunk teljes hosszában mind a 4 „oldalán”, tehát alul-fölül és mindkét oldalon, hogy mindegyik cső minden egyes falvastagsági átmenete nyomon követhető legyen. Ezután átvágtuk a csövek összes kapcsolódási pontját. Lehetőség szerint igyekeztünk kér vagy három irányból, 1/4-es 1/2-es vagy 3/4-es szeleteket kimetszeni az anyagból, hogy minden csőkapcsolat minden irányból jól vizsgálható legyen.
A következő napokban vázanként tucatnyi képen mutatjuk be az adott, feltárt terület jellemzőit, pozitívumait és negatívumait, majd minden vázról egy összegző értékelés olvasható.